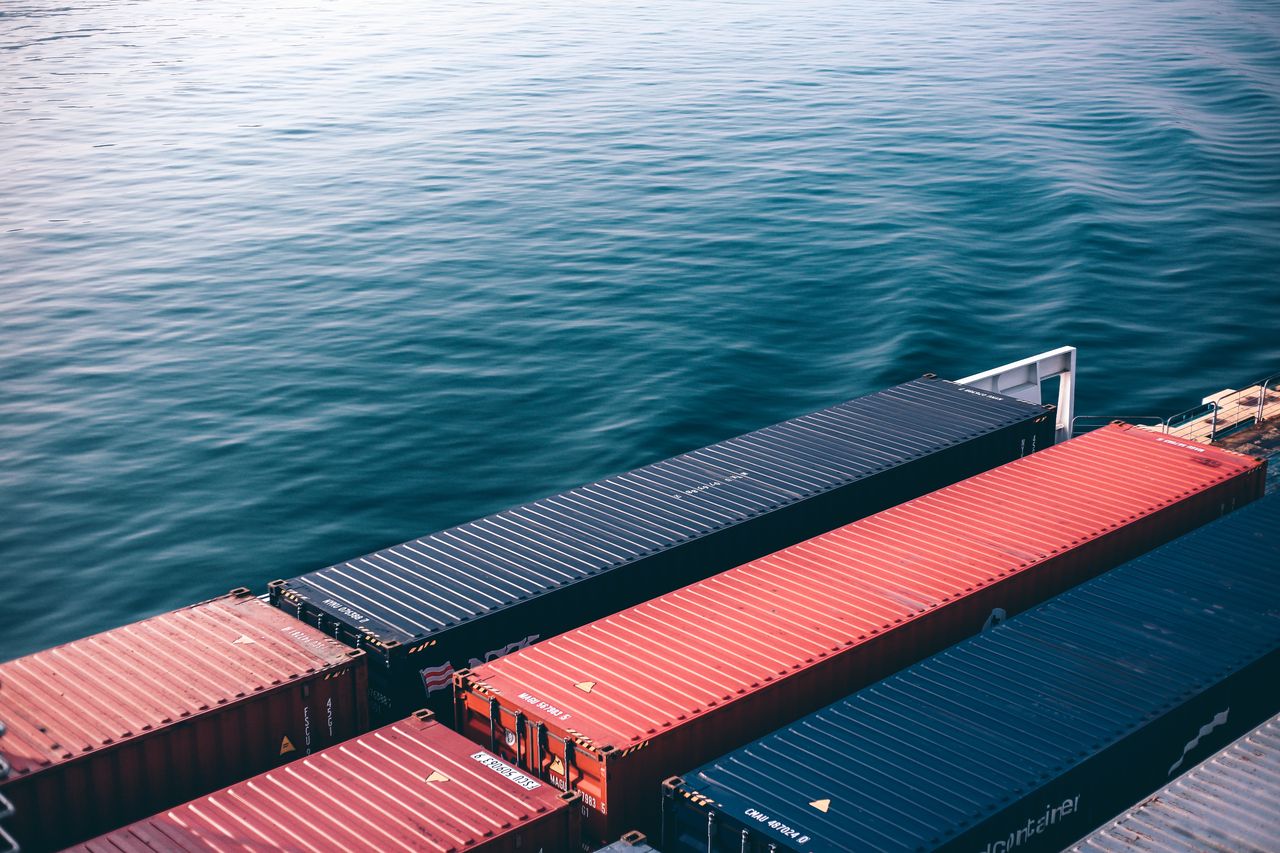
There’s no denying that 2021 has been an extraordinary year so far for importers and exporters. The COVID pandemic unleashed a tsunami of problems, but now there’s another new challenge facing container logistics: the current rollover rate for containers is as high as 20 to 30 percent. And there’s no end in sight for this new trend. This has led to bottlenecks in the supply chain, while you and your logistics team are left waiting for your cargo to arrive. This article explains how container rollovers occur—and how they affect your supply chain.
What are container rollovers?
In simple terms, a rollover occurs whenever your container cannot be loaded onto the ship that you booked. There’s no more capacity on board, so the container is postponed until the next available ship departs. Depending on the destination, this results in a delay of anywhere from a few days to several weeks.
Rollovers are a major headache for logistics teams, but they also result in high additional costs and hassle for shippers and shipping lines. And, unfortunately, they have become a standard fixture in overseas container transport.
When do container rollovers occur?
Rollovers occur any time a container ship is overbooked. This is especially common on high-traffic shipping routes: Container ships from Asia to the United States and Europe, for example, are especially prone to overbooking.
Overbooking makes it harder than ever for forwarders to consign space on a ship, which leads to even more containers being rolled.
Other reasons for container rollovers:
- The ship is rerouted and bypasses a scheduled port of call
- The ship exceeds its allowed tonnage and cannot load all the freight
- Technical problems or material shortages (containers, chassis)
- Customs-related problems
- Missed cut-off deadlines
- Documentation problems
- Natural disasters and other unforeseen circumstances (such as COVID-19)
Due to all these factors, the current rollover rate has skyrocketed. Lloyd's Loading List recently reported that rollovers affect around 20 to 30 percent of all freight from the largest Asian container transport hubs. These are extreme percentages which have greatly slowed down the supply chain.
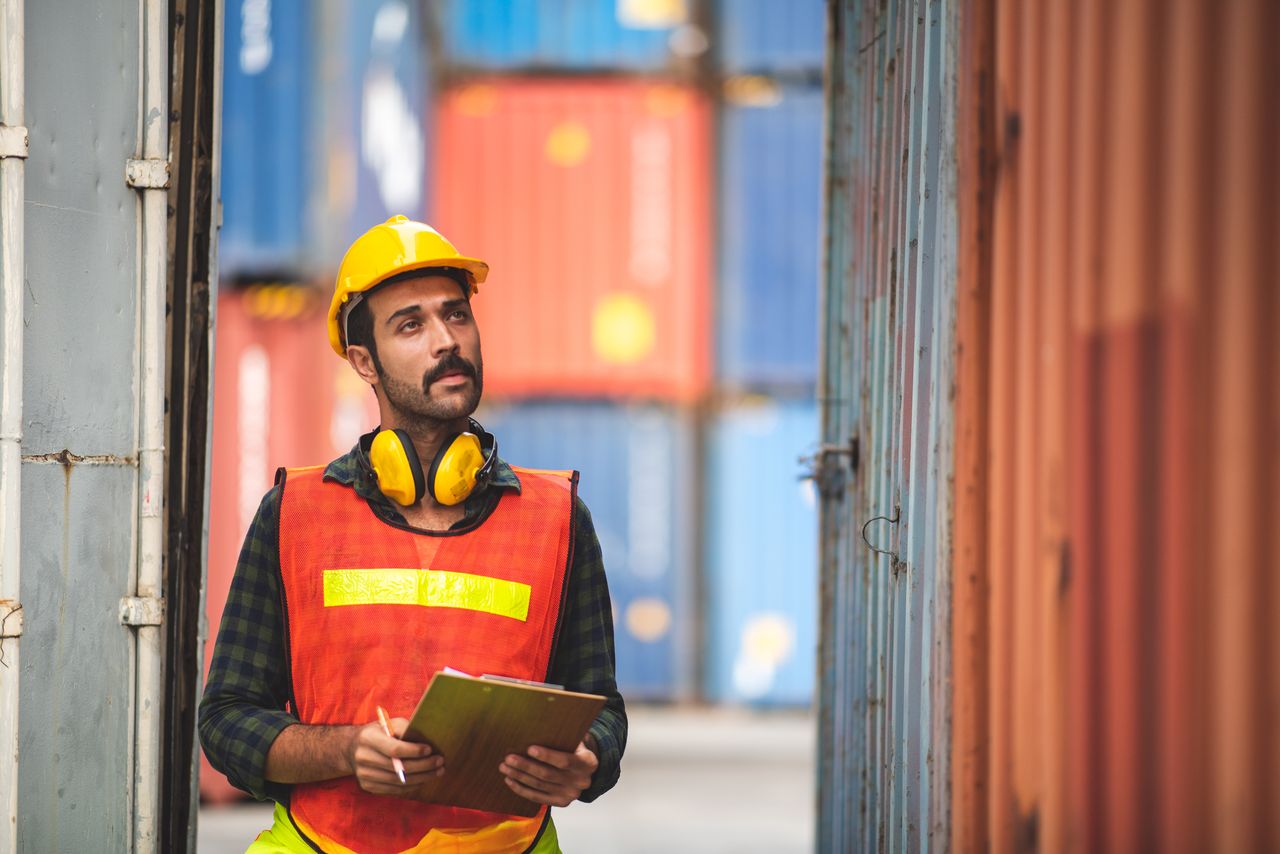
Container rollovers: When mutual trust breaks down
The leading causes for the rise in rollovers at the moment are: material shortages, an increase in transshipments and overbooking. You may be asking yourself: Why are the world’s largest shipping lines struggling so much to get their planning in order? Even the smallest companies work hard to ensure proper inventory management. After all, inventory management is essential for controlling costs, right?
The answer is a bit more complex: Overbooking is usually not a question of poor planning. It is actually a sign of the breakdown in trust between shipping lines and shippers. A shipper books space with the shipping line. And to make sure that their containers can actually be loaded, they always book some additional space on board. Ironically, they do this to prevent their containers from being rolled.
But around 30 percent of the containers they book on paper never actually show up for shipping. As a result, shipping lines can no longer trust the expected volumes or the number of bookings they receive. To prevent empty space on their ships, they accept additional bookings, which means that the supply and demand never perfectly match up.
In the past, shipping lines have also been accused of artificially creating container rollovers to make more money, although they have denied these claims.
Reducing rollovers will require industry-wide change
To rebuild trust between shipping lines and shippers, greater transparency is needed. For their part, shippers must book only the actual volumes they intend to ship. Meanwhile, shipping lines must reassure shippers that their containers will not be rolled.
Maersk has previously tested a system of fines for no-shows and rollovers on containers booked online. This had a positive impact on aligning supply and demand.
How do shipping lines decide which containers to roll?
If a ship is overbooked, it’s up to the shipping line to decide which containers can be loaded, and which will have to be rolled. To make that decision, shipping lines refer to the freight contracts they’ve signed with the shippers. In general, well-designed contracts with reputable forwarders are given priority, which means they encounter fewer rollovers.
What happens when a container gets rolled?
When a container gets rolled, it has direct and indirect consequences that are felt throughout the entire supply chain.
1. Container delays
Rollovers obviously result in delays. According to Bian Wu, Chairman of the Hong Kong Association of Freight Forwarding, delays are usually less than seven days for containers that are rolled at a transshipment hub.
The delays are longer for rollovers that occur at the port of departure. This is because there is a chance that these rolled cargos cannot be loaded onto the next ship departing from that port. As a result, those containers may be delayed for 14 days or more. And, ultimately, it is you and your customers who bear the brunt of those delays.
2. Loss of oversight in the supply chain
Shipping lines do not always keep shippers well informed about rollovers. This leads to even more distrust and confusion in the supply chain. After all, if you no longer have any oversight over expected transit times, there’s no way to properly plan for your cargo’s arrival.
Many shippers say that the rollover itself isn’t the problem: it’s the total loss of oversight. Only in rare cases will shippers be kept up to date on the status of their rolled cargo. That goes for rollovers that occur at transshipment hubs as well as ones that occur at the port of origin. And since carriers generally work according to a weekly schedule, the shipper usually won’t even know until a week later that their container has been rolled.
Jordi Espin, Policy Manager for Maritime Transport at the European Shippers’ Council (ESC), says, ‘It is important that owners always know where their cargo is, and it is unacceptable for customers to be kept in the dark just because of a change in the transport flow. Shipping lines must work to develop customer-focused services instead of just acting as high-volume moving companies.’
3. Price fluctuations
Rollovers also indirectly contribute to fluctuating freight prices. If shippers would be more realistic about how much space they reserve, this would provide a clearer view of supply and demand. As a result, container freight costs would become more stable and predictable.
So, are record rollovers the new normal?
Despite their heavy impact on the supply chain—and on your margins as a shipper or consignor—it looks like rollovers will continue to reach record levels for the time being. The global pandemic has caused numerous shifts in global trade patterns, creating a "new normal" that is not going away anytime soon. For now, it is important to understand the risks of rollovers and know what you can do to minimise them.
When you work with Shypple, what we can guarantee is that you always have full oversight of your containers, even if one gets rolled. Our data-driven platform uses machine learning to track historical rollover rates and transit times, so we can predict future transit times and monitor containers that might be at risk of being rolled. Plus, we keep you informed of the status at every step of the transit. If a rollover occurs, this will quickly be reported to you, so you can take steps to minimise the impact of the delay.
For some practical advice on how to get your containers on board with as little delay as possible, please check out our 7 tips for avoiding container rollovers. If you have any questions or need any help, please get in touch with us!