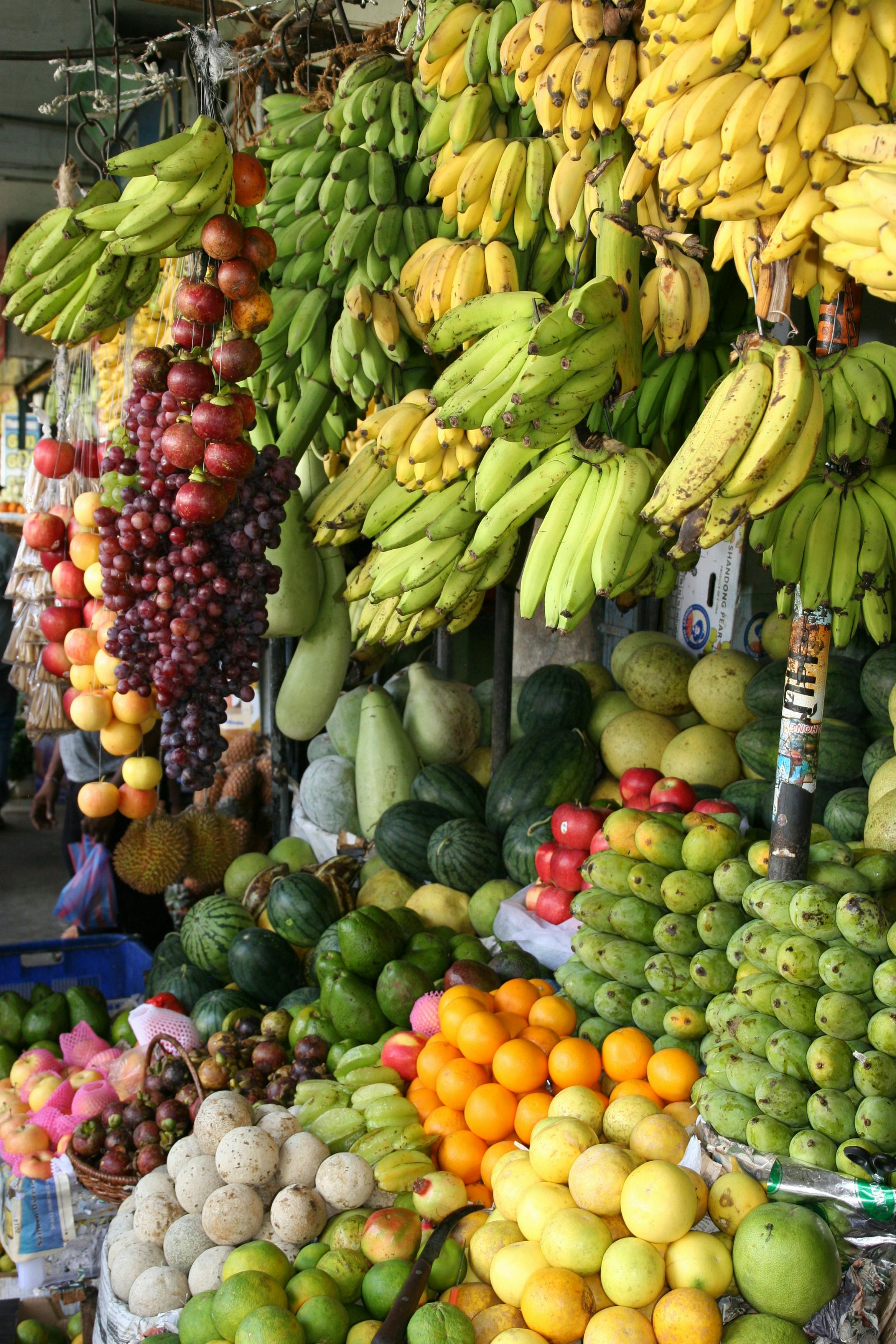
The recent Red Sea crisis, marked by Houthi attacks on shipping, has sent shockwaves through the global supply chain, impacting the maritime routes crucial for international trade. For shippers of perishable goods, particularly food and beverages, the crisis poses a significant challenge. In a world where time is money, delays in transportation can lead to increased costs, spoilage, and potential stock shortages. In this article, we delve into the specific challenges faced by supply chain teams and shippers of perishable goods and explore potential strategies to mitigate the impact of the Red Sea crisis.
The impact on global trade
The Red Sea and Suez Canal play a vital role in global trade, handling approximately 12% of worldwide trade and nearly a third of the world's container traffic. With ships rerouting around the Cape of Good Hope, an additional 3,500 nautical miles are added to their journey. The resulting increase in travel time, estimated at up to two to four weeks, presents a considerable challenge for shippers of perishable goods, where time-sensitive deliveries are paramount.
Immediate impact
The crisis has already led to a surge in container freight costs, with a 15% weekly increase reported in the cost of a 40ft container (in January 2024). The implications are significant, as increased transportation costs could result in price hikes in supermarkets. Additionally, the extended travel times pose a risk of spoilage, particularly for fresh produce, which has a limited shelf life.
Shippers are also grappling with higher insurance payments and increased crew salaries, further escalating operational costs. Most carriers, such as Maersk, have suspended sailings through the Red Sea, citing inflationary pressures on costs, customers, and consumers in Europe and the US.
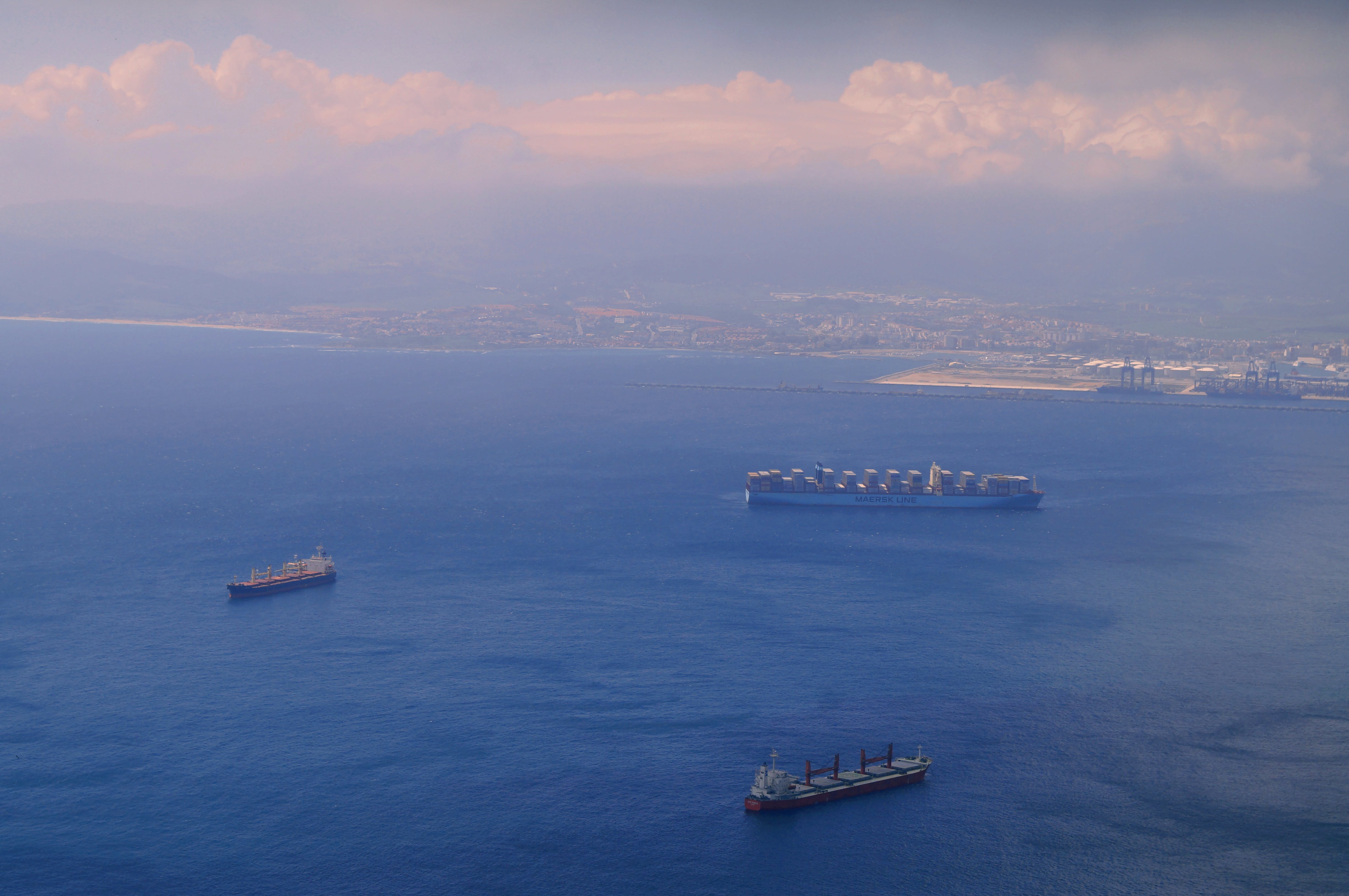
Challenges for the food industry
The food and beverage industry faces unique challenges due to the Red Sea crisis. Italian farmers' organization Coldiretti expressed concerns about the impact on exports of fruits, particularly apples, destined for Asian markets such as Saudi Arabia, India, and the United Arab Emirates. The disruption could jeopardize exports worth millions of euros and affect various segments, including wine.
The UK's largest supermarket group, Tesco, voiced concerns about extended shipping times driving up costs and potentially causing inflation on certain items. The British Retail Consortium acknowledged potential delays in the supply of non-food products from the Far East but emphasized efforts to minimize the impact on food imports.
7 tips for shippers of perishable goods
1. Diversify your routes
Shippers should explore alternative shipping routes that minimize delays. For instance, some companies are opting for sea-air logistics, combining ship transport to strategic hubs and air freight for the final leg. This helps maintain shorter overall transit times.
2. Explore alternative sourcing
Exploring alternative sources for supplies from regions with safer shipping routes can be a proactive strategy. South America, known for producing key ingredients like palm oil, sugar, cocoa beans, and exotic fruits, may become a viable alternative.
3. Stay agile
Conducting scenario planning exercises to anticipate potential challenges and developing contingency plans for various scenarios can enhance preparedness. Shippers need to closely monitor the evolving situation and stay agile in responding to changes. Establishing communication channels with logistics partners and suppliers can help in adapting quickly to emerging challenges.
4. Track your delays and ETAs
Implementing advanced tracking systems that offer real-time visibility into shipments can enhance monitoring. This allows for quick identification of potential delays or disruptions, enabling proactive decision-making. At Shypple, we created a three-layered tracking system just for perishable goods shippers. It includes carrier and terminal tracking, and our dedicated forwarder always checks ETAs, especially if the other tracking systems aren't spot-on.
.png)
5. Manage inventory effectively
Maintaining adequate safety stocks and prioritizing orders through effective collaboration with carrier partners can help mitigate the impact of delays. This includes planning for potential disruptions and having contingency measures in place.
6. Collaborate for risk management
Establishing collaborative risk management initiatives with suppliers, carriers, and logistics partners can enhance communication and coordination. This ensures that all stakeholders are aligned in responding to challenges effectively.
7. Stay informed
Stay up to date on global events and shipping trends. This will help you signal significant developments that might impact your supply chain and proactively tackle them. Our weekly market update is a perfect way to get all of the relevant information delivered weekly to your mailbox. Sign up here.
Looking ahead
The Red Sea crisis presents a formidable challenge for shippers of perishable goods, requiring strategic thinking and proactive measures. The food and beverage industry must navigate through increased costs, potential spoilage, and supply chain disruptions. By diversifying routes, exploring alternative sources, staying agile, and managing inventories effectively, supply chain teams and shippers can minimize the impact and ensure the timely delivery of perishable goods in a world where time is of the essence.
Sources: